The Engender project will take the next step in low energy drying of food and other high value products. In the project an Radial Multizone Drye (RMD) technology will be developed at the pilot-scale.
In short:
- Engender aims to realize a breakthrough in drying of food
- A new drying technology is used: Radial Multizone Dryer (RMD)
- Expected energy savings are estimated up to 30%
Radial Multizone Dryer (RMD)
The Engender project aims to realize a breakthrough in drying of food ingredient materials using a new compact drying technology, the Radial Multizone Dryer (RMD). The Radial Multizone Dryer (RMD) combines high-G and multizone operation to intensify spray drying and offer a cost and energy efficient spray drying solution.
In particular, compared to standard spray drying technologies, the RMD aims at:
- Lower footprint of equipment at equal drying capacity and related reduction of Capex and Opex (equipment size reduced by at least one order of magnitude)
- Improved energy efficiency of ca. 30%
- Significant reduction of air consumption and of exhaust air – such exhaust air, e.g. from spray drying flavours or fragrances, may be heavily polluted and needs treatment. Reduction of the drying air quantity will reduce efforts in exhaust air treatment
- Reduced water consumption in cleaning process (CIP) as a result of the lower footprint (less equipment surface to clean)
- Same or improved product quality. At least cost neutral compared to standard spray drying process (same manufacturing cost per kg of product)
Cost and energy efficient spray drying solution
Efficient drying is achieved by combining radial multizone and high-G operation. The radial multizone operation allows to feed hot air in the radially central zone of the chamber where the droplets are injected and to feed mild temperature air in the periphery where the particles are recovered.
High-G operation is achieved by making use of vortex chamber technology. The mild temperature air is injected through a number of vortex chambers to generate a rotational motion and to control the axial motion in the drying chamber. Droplets injected in the chamber undergo a fast initial drying upon contact with the hot air and are under the action of the high-G force rapidly evacuated to the mild temperature periphery for final drying and recovery.
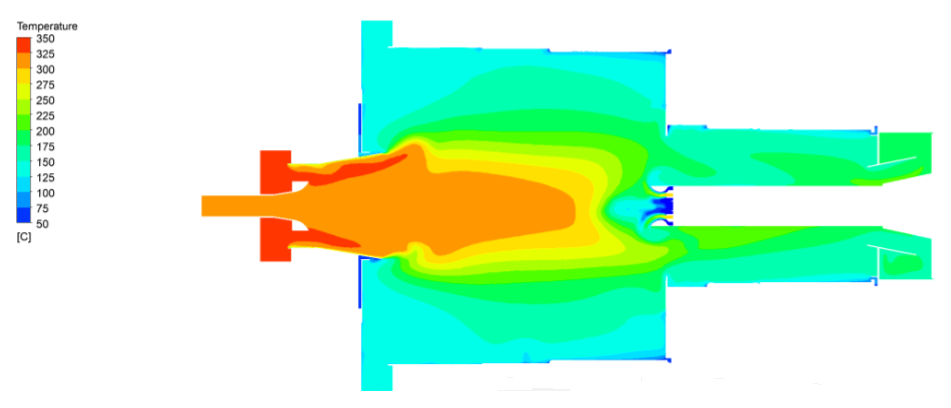
The project will execute validation of several model systems. The long term objective Engender and scaling-up of the Compact Energy Efficient Dryer is implementation of the technology by 2031.
You might also be interested in
Acknowledgement & partners





