The European project cluster aims to approach 80% CO2 emission reduction in the lignocellulose processing chain for cellulose papermaking, compared to the current chain based on kraft pulping by the application of Deep Eutectic Solvents (DESs).
Objective
- To develop a radically new, sustainable and technoeconomically feasible pulping technology for lignocellulose raw materials based on DESs.
- Via DES: to isolate lignin, hemicellulose and cellulose at low temperature and atmospheric pressure for further processing into materials and chemicals with a high added value.
- The PROVIDES project first researched this new type of solvents and it is now followed up by the PRIDES project.
What are Deep Eutectic Solvents?
DESs are composed of two or more components, at least one Hydrogen Bond Donor (HBD) and one Hydrogen Bond Acceptor (HBA), interacting with each other by self-associating forming an eutectic mixture with a melting temperature far below that of its constituents.
The potential of DES to promote mild wood delignification has attracted attention for almost a decade. Delignification requires both lignin depolymerization and dissolution. In this leaflet we descibe the DES delignification mechanism.
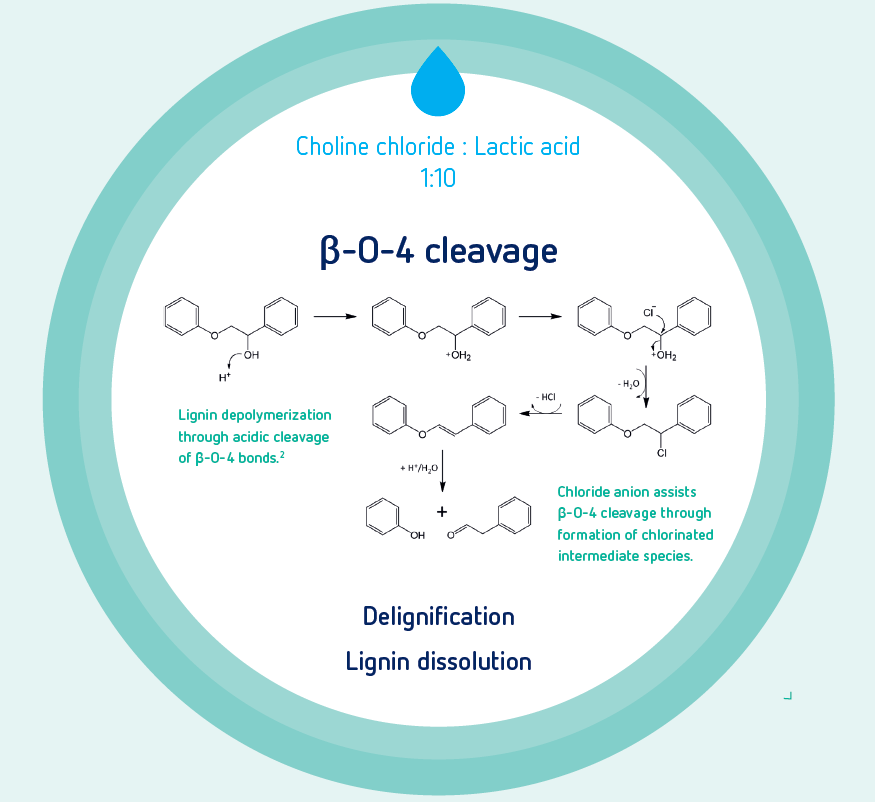
Public summary
A wealth of knowledge and understanding of biorefinery
In nine years, the consortium of the Deep Eutectic Solvents in Papermaking project has gained a wealth of insight into biorefinery and the possibilities for sustainable pulping. Nevertheless, the decision has now been made to terminate the project. The decision has been made not to proceed with the construction of a pilot plant. Several consortium partners will, however, independently continue to work with research results. Further process optimization and expansion of their product portfolio are their goals.
The pulp industry processes wood into fibres from which paper can be made. The traditional Kraft pulping process as currently widely applied in the European pulp and paper industry is a very effective and CO2 efficient process, as energy and chemicals are recycled. It isolates high quality fibres with hemicellulose as important strength enhancer. The remaining lignin serves as a sustainable energy source to feed the process in which pulping chemicals are recovered.
A high bar
With such a well-functioning process, the bar for achieving a better pulping process is quite high. Climate change calls for even more efficiency, though. In the upcoming decades fossil-based chemicals need biobased replacements, thus putting additional pressure on natural resources. The lignocellulose pulping concept is thought in principle to hold the opportunity to make this transformation. This requires a pulping process that yields lignin that can be easily isolated from the pulped fibres, in a quality that can be converted into biobased chemical building blocks. Moreover, significant energy saving during the pulping process would allow the lignin side stream to become available for alternative applications.
Therefore, the development of more sustainable methods of fractionation and conversion of biomass into added value materials and chemicals is of the utmost importance in the biorefinery approach. A key strategy was seen in the application of more selective and benign solvents, in which the use of Deep Eutectic Solvents (DES) stands out.
The application of DES would be an innovative and green technology with high potential to fractionate biomass components at lower cost and with reduced energy consumption. The capacity to dissolve and extract lignin selectively and at high quality were promising to achieve higher sustainability.
This theoretical promise of being able to extract cellulose at low temperature and pressure and with mild, natural solvents was attractive enough for the consortium to start cooperation. The consortium explored which of the mild DES solvents would be best to isolate lignin from wood. It examined the mechanism behind DES delignification, designed a process for recovering the DES, analysed the potential of the various product streams and made thorough mass and energy balances. All this relevant information contributed to the answer to the main question: would the process work so well that it could replace current Kraft pulping processes?
Treasure of systemic understanding
A wealth of systemic insights into all aspects of pulping via biorefinery has been obtained by this knowledge development and modelling. Bonuses of the DES process are the good quality of the lignin that the alternative process produces, the potential much smaller scale at which the process could be economically operated, and the much lower water use compared to the Kraft pulping process. The lower water consumption of the DES process is due to a significantly lower water content in DES compared to the Kraft cooking chemicals. Additionally, the DES process concept integrates multiple advanced separation steps. This results in a clean water stream that can be effectively reused in the process.
The high expectations of significant energy and CO2 savings, however, did not yet materialize. The energy consumption and environmental footprint of the alternative small scale process turn out to be comparable to the large scale Kraft pulping process. Moreover, the main product, cellulose, is obtained in a pulp quality that resembles sulphite pulp and doesn’t live up to Kraft quality standards. It also proved difficult to find an optimum between recovery processes and the value of recovered DES and any additional products to be valorised. Each additional separation step is expensive, which is hard to balance with the value of the total product slate.
Moving forward with results
All in all, the consortium therefore decided not to proceed to building a pilot plant for this process. It is a remarkable step; after all, a rational decision on whether a high follow-up investment is worthwhile is far from obvious in innovation processes.
The decision not to proceed in no way means that the project has little yield. It only means that this alternative process has been abandoned as a bulk process for the entire industry. Individual consortium partners do go forward with the results. Several products produced in the investigated processes are very promising – albeit for more specialized products. One is pure cellulose that could be used for dissolving cellulose. Other process conditions yielded cellulose that easily degraded into sugars. The lignin isolated from by the DES process revealed interesting functionalities for allowing conversion into chemicals. All these directions are beyond the current scope of most companies in the pulp and paper industry.
Positive cooperation
The cooperation in the research project and its organization are rated very positively by the partners. The project could always be adjusted to the needs of the industry. The insight in biorefinery processes, its possibilities, and impossibilities, has increased enormously thanks to this project. This is a very valuable fact, because biorefinery will prove very important for the future of the process industry.
You might also be interested in
Acknowledgement & partners
The authors would like to thank the members of the Institute for Sustainable Process Technology (ISPT) “Deep Eutectic Solvents in the pulp and paper industry” consortium for their financial and in kind contribution. This cluster consists of the following organisations: BASF, CTP, CTS Twente, ISPT, MM Board & Paper, Mid Sweden University, Mondi, Sappi, Stora Enso, University of Aveiro, University of Twente, Valmet Technologies Oy, VTT Technical Research Centre of Finland Ltd, WEPA and Zellstoff Pöls. This project received funding from TKI E&I with the supplementary grant 'TKI-Toeslag' for Topconsortia for Knowledge and Innovation (TKI's) of the Ministry of Economic Affairs and Climate Policy. More information can be found on https://ispt.eu/programs/deep-eutectic-solvents/.














