This project covers the design, realization and exploration of the Hydrohub MegaWatt Test Center at the Zernike Campus in Groningen.
In short:
- Topsector Energie called upon the industry to start working on testing large-scale electrolysers in an industrial setting
- The MegaWatt Test Center can be used to perform such tests with water electrolysis at MW scale
- This is unique since manufacturs of electrolysers usually don’t offer transparency
- It is expected 2 to 3 % operational efficiency gain can be achieved
The MegaWatt Test Center is a stepping stone towards the future gigawatt scale production of sustainable hydrogen by the process industry. The open-innovation infrastructure will be used to do research and perform series of stress testing at MW scale with water electrolysis (both Alkaline and Proton Exchange Membrane (PEM)).
Material and component suppliers for membranes, anodes, electrodes, pump, and so on, are facilitated to test the impact of their products. Since manufacturs of electrolysers do not offer this transparency, this is a unique feature.
Hydrohub Innovation Program
The MegaWatt Test Center is a part of our Hydrohub Innovation Program and therefore aligned to other hydrogen initiatives by the process industry and academics.
Also interesting to read
- Interview with projectleader Robbert van der Pluijm about the impact of the MegaWatt Test Center
- Ontwerp waterstoffabriek gaat de wereld over
Or join our LinkedIn-community on hydrogen.
Advanced process control
Early 2021 TKI Energy & Industry granted the project with a first addition to the original project. The addition involves advanced process control and will be executed in parallel to the current Hydrohub MegaWatt Test Center. The consortium is happy to announce a new partner in advanced process control: Yokogawa, manufacturer of equipment for the process industry.
Production of hydrogen from renewable power sources requires dynamic operation of electrolysers. The new additional, dedicated research project models and researches the impact of variable operation on electrolyser performance and the electricity grid. Optimal control strategies will be developed with the goal to improve overall operational efficiency.
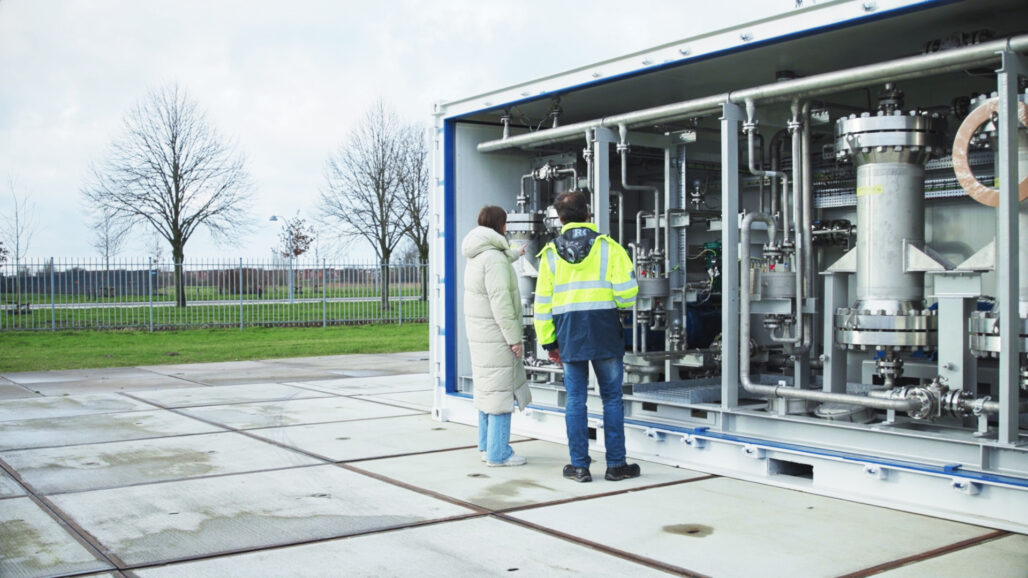
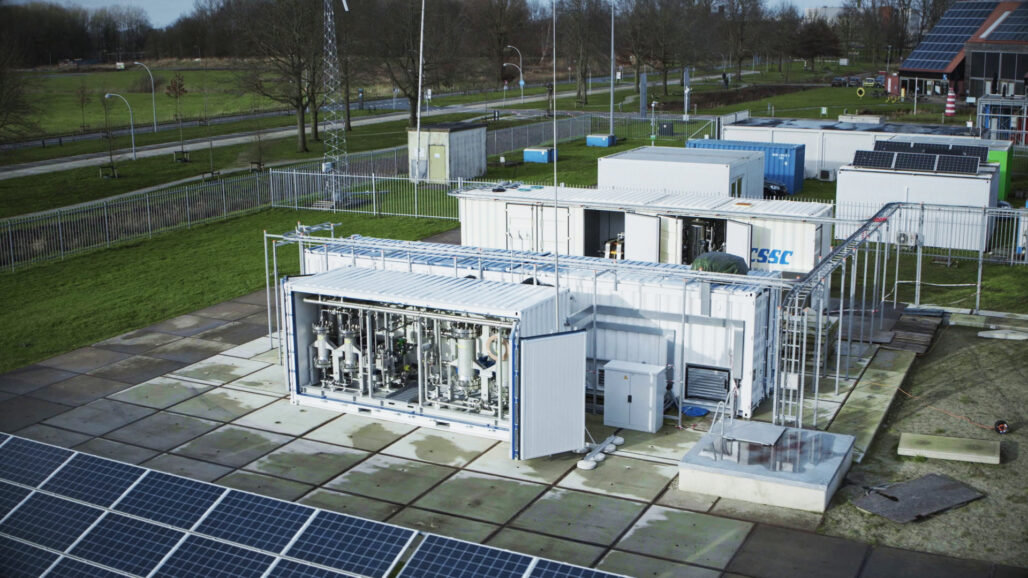
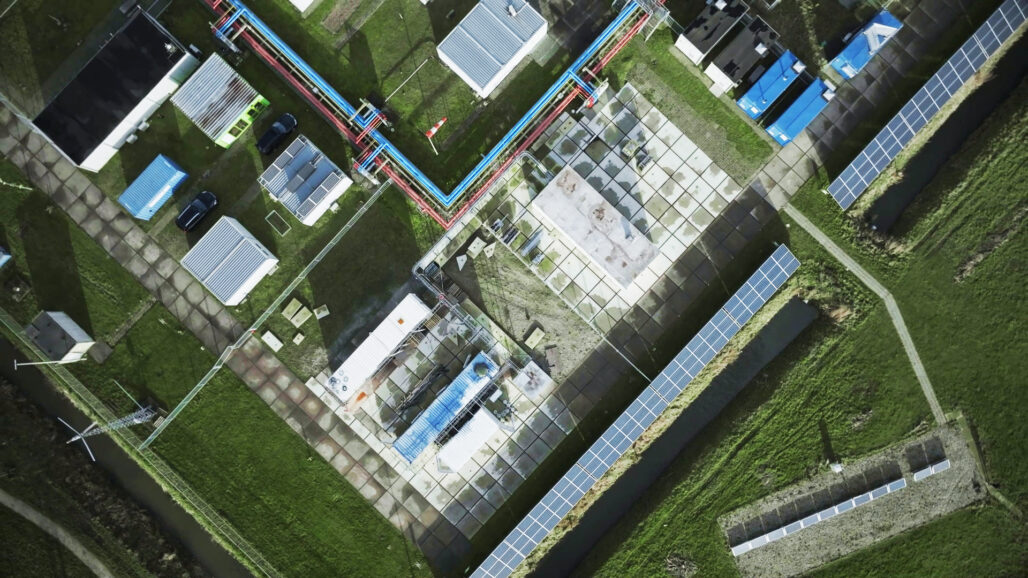
The MegaWatt Test Center at EnTranCe, Groningen
2-3% operational efficiency gain
Advanced process control has been implemented in other industries successfully to improve efficiency and optimize multiple parameters simultaneously by considering the interaction, process dynamics and buffering and release of mass and energy in reactions. In this case of the flexible production of the green hydrogen, this is a totally new way of process control for electrolysers.
It is expected that by applying advanced control strategies 2 to 3 % operational efficiency gain can be achieved. The research proposed in this project is aimed to research, model, and test this potential efficiency gain on the PEM unit.
You might also be interested in
Acknowledgement & partners
Dit project is medegefinancierd door TKI-Energie uit de Toeslag voor Topconsortia voor Kennis en Innovatie (TKI’s) van het ministerie van Economische Zaken en Klimaat









