In today’s world, plastic has become indispensable. The material plays an important role in almost all aspects of modern society. As a detrimental side effect, plastic waste can be found all over the world. ISPT and DPI recently took the initiative for the Circular Plastics Initiative, in which parties along the entire chain work together to create a more sustainable, circular life cycle of plastics. Among them is polymer producer Dow Benelux under the leadership of president Anton van Beek. We asked him about his vision on circularity in plastics, and Dow’s role in this.
The Circular Plastics Initiative is a broad-based international cooperation in which a variety of parties work closely together. It includes plastic producers such as Dow, plastic users such as LEGO, waste processing companies, governments and NGOs. That’s why we first ask the question:
Who is responsible for the problem of plastic waste?
Van Beek: “I am, you are, we are all responsible! Together we have created this waste culture that has to come to an end. That is why society is moving towards a circular economy in which waste – and in our case that’s plastic waste – becomes a resource again. As a plastics producer we are working hard on this. But in the end, we have to do it together. The same goes for plastic as for the beverage can, the cigarette butt, you name it. It’s all waste that should not be found in the streets, nor in nature; it has to end up in the waste bin. The challenge for society as a whole is to change that. We all have to separate our waste and make sure it gets back to the producer.”
Shouldn’t society be looking for alternatives to plastic?
“Of course, it can make sense to develop alternatives. But as one of the largest plastic producers in the world, we are convinced that in many cases plastic is the right product. It is light, functional, and relatively inexpensive. Look at food packaging, which for us is a very important market. There, it’s all about food safety and health. Consumers want to be able to buy their fruits, vegetables and meat as fresh as possible, and plastic protects very well against ageing and decay. Some other materials can also offer such functionality, but the environmental impact of plastic is usually smaller because you only need very little material that is also made with an extremely efficient production process. Plastic often has the lowest energy per functional unit – and therefore the lowest carbon footprint for the same functionality. That matters throughout the entire logistics chain”.
Plastic often has the lowest energy per functional unit – and therefore the lowest carbon footprint for the same functionality.
How does Dow contribute to solving plastic waste?
“We are working on all fronts to achieve circularity in plastics. It is now the central concept of our product development. In addition, we participate in the sector-wide Alliance to End Plastic Waste. Over the next five years, 1.5 billion dollars will be available and Dow will make a substantial contribution. We are doing our best to raise public awareness and promote reuse and recycling. But the goal is also to develop solutions for the separation, processing and actual reuse of plastic waste. This dovetails with the Circular Plastics Initiative in which all relevant players in the value chain are at the table. Including NGOs, which are of course very important in this matter. This setting is very valuable to Dow; for us it is difficult to organize this otherwise”.
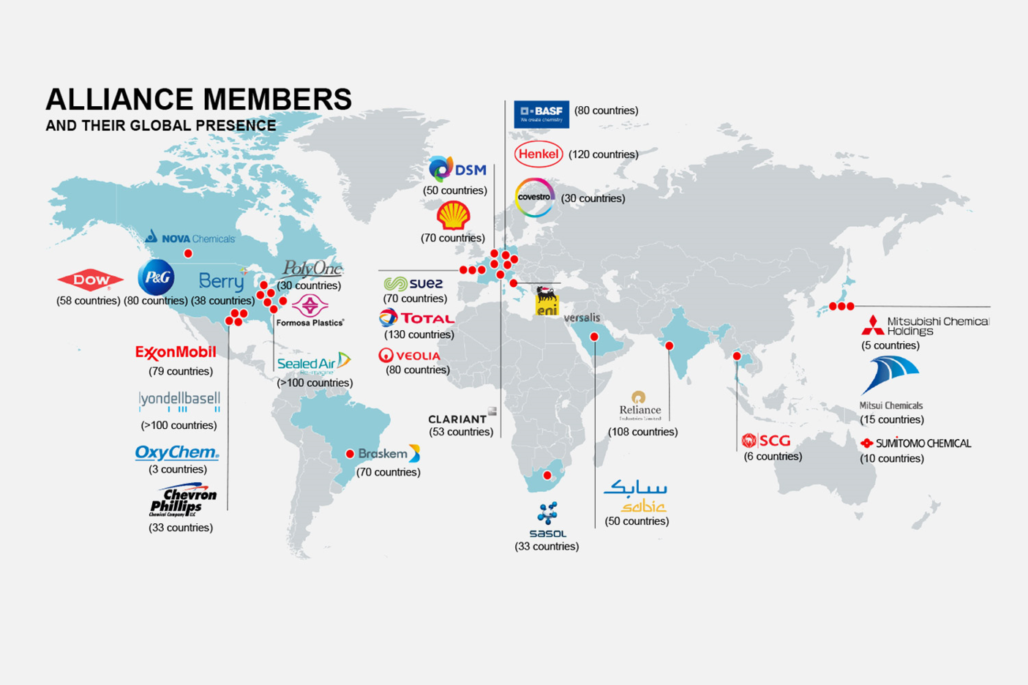
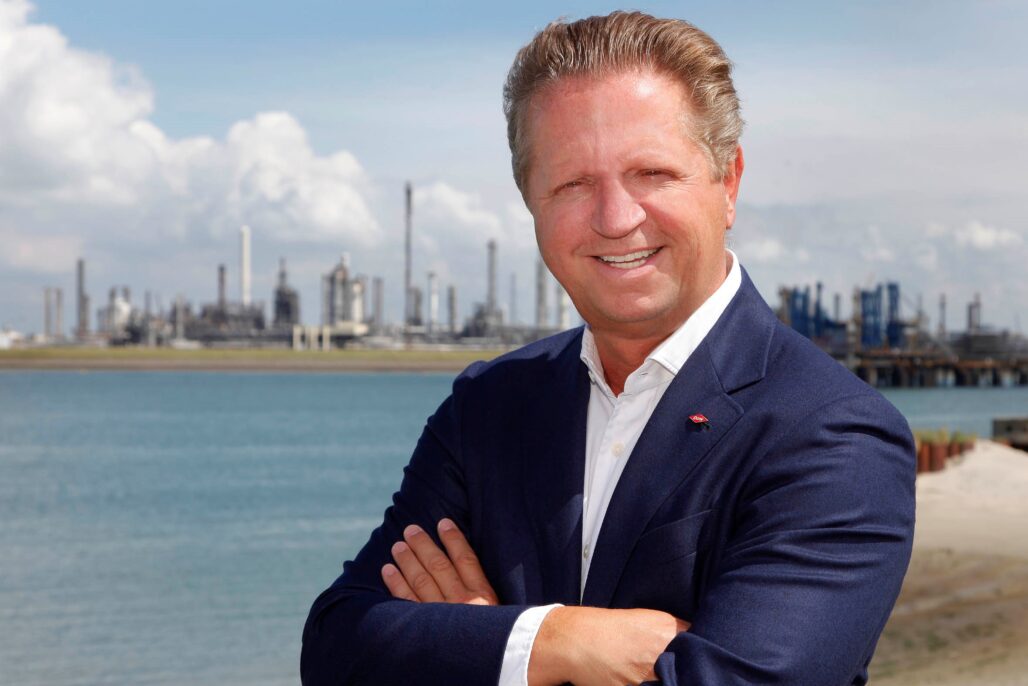
So what’s the biggest challenge for Dow?
“What matters is that we, as producers, consider the full life cycle of our plastic. At Dow, we are already used to considering our customers’ wishes and requirements – and even further down the chain, the wishes of the customers of our customers. Now that we also have the waste phase in sight, we develop plastics that a priori lend themselves to reuse. In this ‘design for recycling’, we have already made significant steps forward. One example is our AGILITY low density polyethylene (LDPE) products which can contain up to 70% recycled material”.
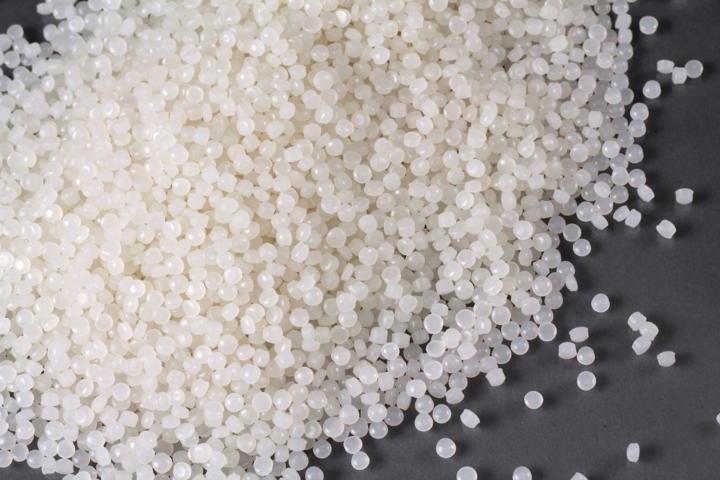
“This example refers to mechanical recycling where plastic is separated from the waste stream, crushed and reprocessed into a plastic product. With several high-grade plastics, such as those for food packaging, this approach does not work. On the one hand specific functionalities, such as protection against oxygen, are lost in the process. On the other hand it is difficult to get rid of contaminants related to the collection and sorting process in such a way that the quality requirements for food safety are met. The solution here lies in chemical recycling, which we also call feedstock recycling. Realizing this is now considered the most important challenge”.
“In feedstock recycling, we break down the plastics on a molecular level, down to its molecular building blocks. From those we can then make polymers again. This results in new plastics that, although recycled, are indistinguishable from the brand-new material that we call virgin plastic”.
What is the challenge of chemical recycling?
“The technology is available; polymers can be broken down by gasification or pyrolysis. We perform research on gasification ourselves and we cooperate with others in the field of pyrolysis. Briefly put, pyrolysis is oxygen-free combustion that produces an oily liquid from which we can make plastic – just like from petroleum”.
The main concern is to improve efficiency for economic reasons
“The main concern is to improve process efficiency so that also from an economic perspective feedstock recycling will be a really promising technology. So our goal now is to develop the most efficient feedstock recycling process available. Together with ISPT, DPI and other parties, we hope to be able to set a standard that will enable us to be a global leader”.
What are the chances that this will work out?
“I am quite confident. The conditions are relatively favourable – I think here in our part of the world we will be the first to make the transition to the circular economy. We have the money and national and European governments want to lead the way. However, if we as a small country with limited resources want to play a relevant role here, we have to join forces. The Circular Plastics Initiative does that very well and, as far as I am concerned, deserves the opportunity to tackle this on a large scale. ISPT and DPI are able to stay close to the industry with an organizational model that makes it possible to work quickly, concretely and result-oriented. That is what we need to be able to solve this problem!”.
This is the first interview in a series of interviews with parties throughout the plastic value chain, participating in the Circular Plastics Initiative. In the second interview Martine Brandsma, director of NTCP, talks about application-driven recycling of plastics.
Acknowledgement
This project is co-funded with subsidy from the Topsector Energy by the Ministry of Economic Affairs and Climate Policy.