- Breaking research in ‘CORESYM’ report reveals potential for symbiosis between chemical and steel industries
- Key findings show re-use of waste gas from steel industry can lead to drastic reduction in European CO2 emissions and mitigate other environmental impacts
- Report reinforces the need for policy intervention and technological investment to move towards a sustainable European steel industry
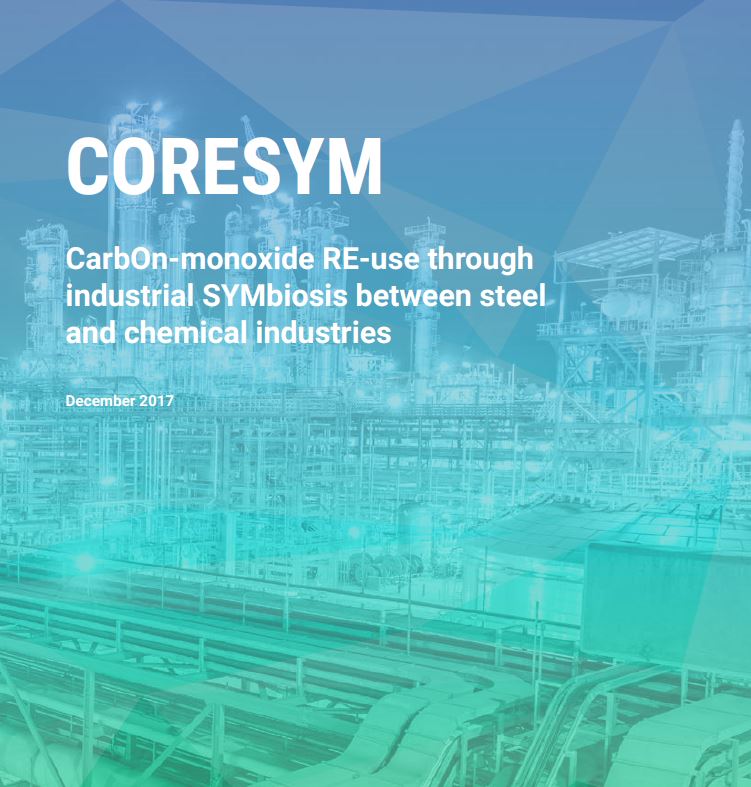
Amersfoort, 29th of November 2017 – The steel industry can drastically reduce CO2 emissions by recycling part of its carbon emissions in the chemical industry. This will in turn help the chemical industry lower its consumption of natural gas and oil. Eventually this development could lead to a reduction of European CO2 emissions of 57 million tons per year, that is 1,3% of the total CO2 emissions in Europe. To realise this perspective the industry will need financial support from the national governments as well as the European Union.
This is the conclusion brought forward in the ‘CarbOn-monoxide RE-use through SYMbiosis between steel and chemical industries (CORESYM)’ report. The report shows the results of a study, carried out by sustainability consulting firm Metabolic and researchers of the University of Groningen commissioned by the Institute for Sustainable Process Technology (ISPT), Nuon, Tata Steel, AkzoNobel, Dow, Arcelor Mittal (Gent, Belgium) and the TKI Energy and Industry.
During steel production, waste gas is released; this gas consists of 18-30% carbon monoxide (CO), for 15 to 25% of carbon dioxide (CO2), and further of nitrogen and a small amount of hydrogen. Steel factories are currently burning the carbon monoxide in powerplants, converting the CO into CO2. This is actually an absolute waste because to chemical companies carbon monoxide is a valuable resource. Furthermore the burning of carbon monoxide produces twice the amount of CO2 compared to the burning of coal.
Steel production concerns large volumes of carbon monoxide. That is why the obvious choice would be to use it to produce large quantities of basic chemicals. In the short term the production of hydrogen comes to mind. This will save natural gas, because hydrogen is currently produced using mainly gas. Carbon monoxide can also be used for the production of methanol, ethanol, a replacement for naphtha (a raw material for e.g. poly ethylene and poly propene) and synthetic fuels. Put together all of these potential uses for carbon monoxide will lead to a reduction in CO2 emissions within the steel industry of 20 to 35%, compared to the current situation. This means that carbon monoxide will no longer be burned while the chemical companies simultaneously save on fossil fuels, which will also lower their dependence on the import of fossil fuels from countries outside of Europe. In the long term the steel industry could potentially start using synthetic materials beside cokes as a carbon source for the production of steel. This way the steel industry and chemical industry will be able to bring carbon into a cycle and by doing so bring a circular economy one step closer to realisation.
A challenge is still posed by the capability to efficiently separate CO from large volumes of steel gas; although the development of the technology needed to achieve this has reached a reasonably advanced stage. The separation process also delivers a flow of relatively pure CO2 directly suitable for other applications or for storage.
The implementation of large-scale re-use of steel gas to products requires an active and involved government. With new collaborations and investments, the technology can be further scaled up to make it market-competitive. Operational grants by the SDE+ have shown that they can greatly accelerate affordable sustainable generation of electricity by means of windmills. With comparable support this same impulse can be provided to the surplus- gas re-use in the steel industry. Per euro invested this will also yield a significant CO2 emissions reduction compared to investments in electricity generation. Next to that it is also important that the products made from steel gas are included in the new EU-guidelines for renewable energy for the time period between 2020 and 2030 (RED II) so that these products will be recognised as sustainable.
‘’Eventually circular carbon will yield more CO2 – emission reduction per euro than any other solution, including the capture and storage of CO2. The Dutch government should invest in new technologies, eg. the re-use of steel gas, rather than spend this money on CO2-storage’’, says Tjeerd Jongsma, director of the ISPT.
“In Germany we are already working on a project to convert CO2 from steel production into useful raw materials for chemistry. With the knowledge and expertise available in the Netherlands, we can also use this technology here to make the difference” says Marco Waas, Director RD&I and Technology at AkzoNobel.
‘’For the Netherlands, re-use of steel gas could mean a decrease in CO2 emissions of five million tons per year. This is one-tenth of the Dutch target for emission reduction in the industry’’ according to Andreas ten Cate who coordinated the study at the ISPT.
‘’We view this report as a first step towards the re-use of steel gas. We still have many things to figure out, among other things whether or not re-use can prove itself compared to other technologies that can reduce CO2 emissions’’ says Cock Pietersen, Manager Energy Procurement at Tata Steel in Ijmuiden.
‘’We are ready to build an ethanol factory that will strongly reduce the emissions of steel gas. For this we will need support however’’ according to Eric de Coninck, LIS Project Manager at Arcelor Mittal in Gent.
‘’Based on carbon monoxide we expect to be able to produce a replacement for naphtha and use carbon monoxide in this way for the production of synthetic materials. We would also be willing to buy methanol from a third party that produces it based on carbon monoxide extracted from steel gas’’. Declares Kees Biesheuvel, Innovation Manager at Dow in Terneuzen.
The ESTEP (European Steel Association) views steel gas re-use as described in the CORESYM study as an important contribution in moving towards a sustainable European steel industry.
At the time of writing this article it was announced that on the 28th of November 2017 the European Parliament’s Committee on Industry, Research and Energy (ITRE), approved the re-use of CO from steel gas into so called “recycled carbon fuels” in Europe.