Roller Drying as a drying method is often applied in the process industry, it is also the preferred option for drying wet algea. In the project Roller Drying for Algea the ISPT joins forces with PhyCom, Andrits and Vito to improve the roller dryer technology specifically for algea. The project was successful in that it did not only yield an increase in the quality of the end product and the volume, but also a decrease in the cost.
Algea, something to look into
Components recovered from the algea can be used for food or as a base for chemicals. It’s a versatile resource and algea are very cheap, but the roller drying process is extremely energy intensive. The extraction of raw materials with high added value from algae is therefore especially suitable for the application of this improved technology, as an alternative to, for example, the relatively expensive freeze-drying.
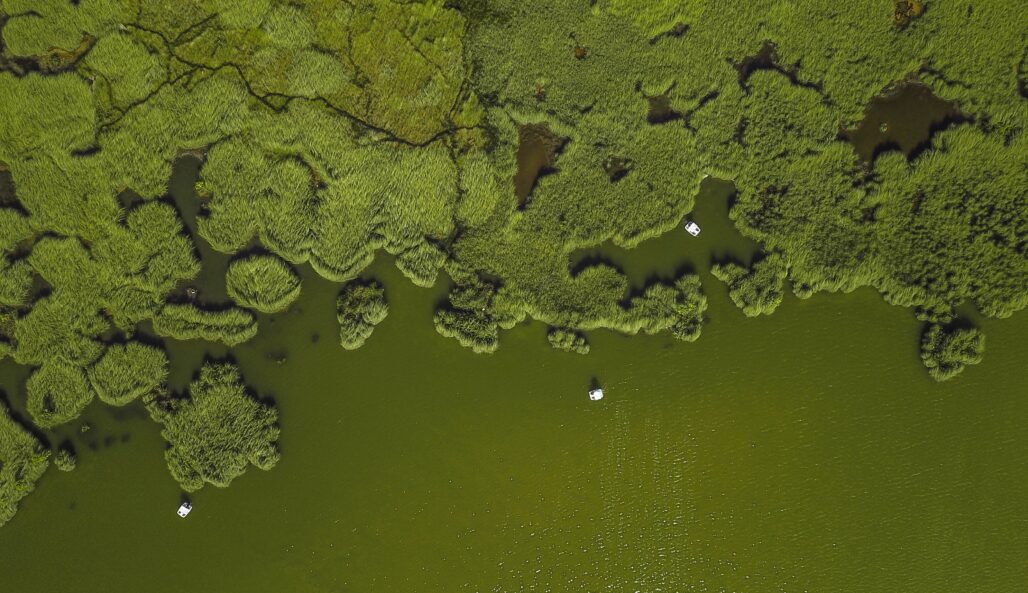
Bringing roller drying to a higher level
The researchers experimented with a type of nozzle that sprays the product on the roller, a thin film will then easily evaporate. The project investigated the possibilities of this application method, the optimal thickness of the thin film, the nozzle profile, working with one roller or two, and the possibility of working under low pressure. Under low pressure, water evaporates at lower temperatures, which protects the vulnerable substances from degradation.
Innovation leads to progress
The best results proved to be achieved in a design that included two revolving rollers, with a thin liquid film between them. The production speed increased by a factor of three, with improved quality and safety of the dry matter and it resulted in a 15 to 20% decrease in energy use. Moreover, the installation can be built much more compactly, and therefore at a lower cost.
Challenges and future steps
There are still design issues that will have to be solved, such as protecting the entire installation against pollution that is caused by pulverized algae. The atmospheric variety is ready for the next steps, including scaling it up to a 20 times bigger installation and commercialization by the technology supplier. The vacuum version of this roller dryer will be tested in a follow-up project. In this project there will be special attention for the supply and removal of process streams in the pressure chamber.